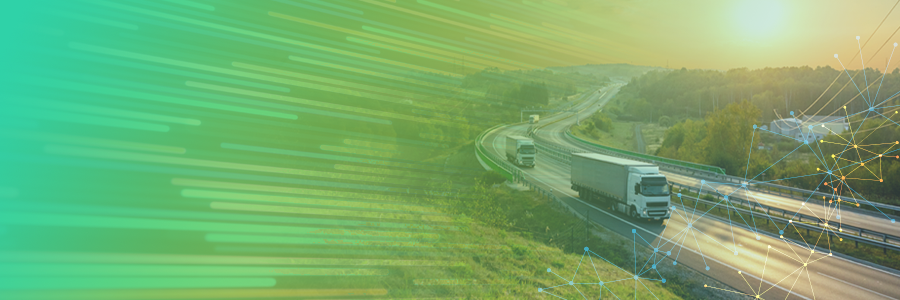
In the transportation and logistics (T&L) industry, there is a truism: “if the wheels don’t turn, you don’t earn.”
It’s a simple statement, but an accurate one. It also speaks to the fact that 20% of any T&L fleet vehicles incur unplanned downtime due to accidents alone and that overall vehicle downtime costs fleets $3.3 billion USD each year.
The most obvious reason for supply chain trucks to be sidelined is unexpected repairs or scheduled maintenance, which happens more often than you may think. It’s been shown that truck breakdowns which require roadside assistance occur every 10,000 miles (approximately 16,100 km).
However, as evidenced in the latest SOTI report, Mobilizing the Delivery Workforce: State of Mobility in Transportation and Logistics, downtime isn’t limited to truck or vehicle issues.
But it is a good place to start when determining how technology can reduce supply chain interruptions to keep wheels turning and businesses earning.
wHAT ARE THE DANGERS OF DOWNTIME IN THE T&L INDUSTRY?
Find out in your free copy of Mobilizing the Delivery Workforce: State of Mobility in T&LWhen Trucks Go Down, Costs Go Up
On almost any street in any city and at nearly any given time, there’s a truck making a delivery of some sort.
When trucks are on the road, T&L companies make money. When they’re not, they’re losing money due to the cost of downtime to an average of $448 to $760 USD per vehicle per day.
So, as efficient as the supply chain currently is, it can be even more efficient – and by extension more profitable – by mitigating against unplanned maintenance or preventing poor vehicle performance.
Take tire pressure, for instance. A tire that’s 10% under-inflated can result in a 1% drop in fuel economy. When fuel accounts for 50% of the variable costs of running a fleet, maintaining tire pressure lowers expenditures and increases driver and vehicle safety too.
This is where technology comes in. Sensors on the truck can alert the driver of the issue, who can then take the corrective action of pulling into a service station and inflating the tire.
Beyond unplanned maintenance, there are other reasons why the supply chain may grind to a halt and impact the cost of downtime. Fortunately, technology can help with those too:
- Gridlock: Each year, the T&L industry loses $63 billion USD in fuel, labor costs, and vehicle wear and tear just from sitting in traffic. In terms of time, collectively 996 million hours are lost, which equals 362,243 drivers sitting idle for a full year. Real-time traffic and route optimization can help drivers avoid problematic areas, and supply chain businesses keep costs down.
- Device downtime: Scanners, tablets, smartphones, apps and warehouse printers all play an important role in ensuring on-time shipments. Globally, T&L workers lose 3.3 hours per week due to device downtime. Over the course of a month, downtime becomes a sizable and costly waste of resources. Since many of these devices are in the field, shipping them back for repairs isn’t an option. A diagnostic help desk solution made for mobile devices allows IT departments to remote control the device and resolve the issue, whether it’s across town or around the world.
- Lack of system integration: The very nature of the supply chain dictates that goods get handed off from one part to another in a timely manner. Yet when it comes to information, nearly 33% of respondents in Mobilizing the Delivery Workforce: State of Mobility in Transportation and Logistics say updated information not being shared across systems is a concern. System integration solves this by ensuring the right data gets delivered to the right people and the right devices at the right time.
Customers Aren't Interested in the Cost of Downtime
Collectively, global consumers spent $26.7 trillion on e-commerce purchases in 2020. And for every purchase, whether it’s groceries, cleaning supplies, hobby items, medicines or school supplies, the customer deemed them to be essential, meaning they had to be delivered on time with no exceptions.
For 98% of T&L organizations, a broken-down truck, a faulty warehouse printer or an unresponsive app – which delays shipments – occur on a weekly basis. But to consumers, they’re unacceptable.
That’s why it’s necessary that all touchpoints in the supply chain minimize the cost of downtime as much as possible.
Mobilizing the Delivery Workforce: State of Mobility in Transportation and Logistics takes a detailed look at all the dangers of downtime within the industry. It also touches upon the top business concerns organizations face when trucks aren’t moving.
It’s a must-read for any T&L organization interested in keeping the wheels turning and keeping the business earning.